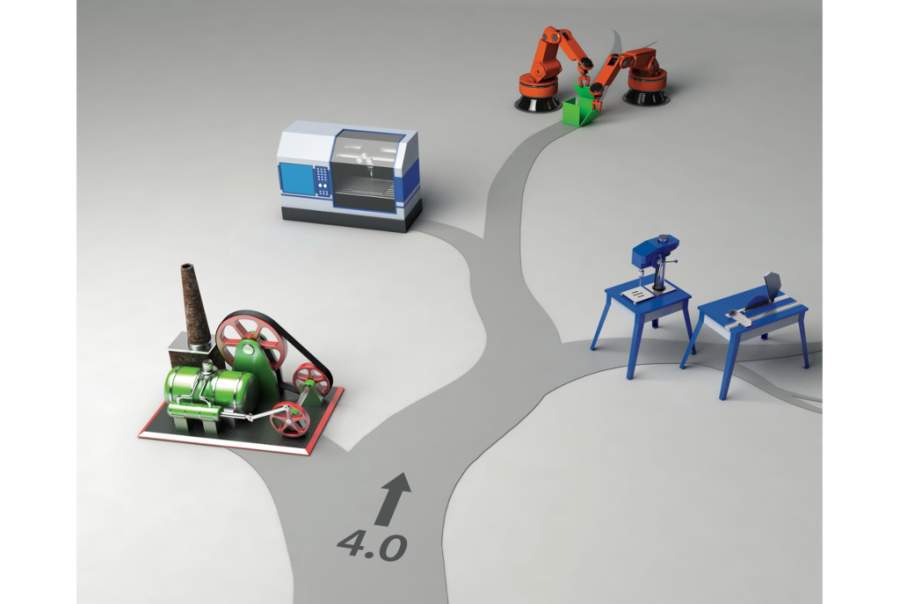
Digit-All-isierung
Neue Techniken verschweißen alle Unternehmensbereiche zur Industrie 4.0
Programmierte Maschinen lernen, spontan mit ihresgleichen und mit menschlichen Kollegen zusammenzuarbeiten. Wenn dann auch noch die Fertigung nahtlos mit Buchhaltung, Vertrieb und Kundendienst zusammenwächst, ist das Buzzword von der vierten industriellen Revolution durchaus gerechtfertigt.
Kennen Sie Industrie 3.0? Und die Vorversionen? Die Vorläufer der aktuell ausgerufenen Industrie 4.0 sind schnell charakterisiert:
Dampfmaschinen und Wasserkraftanlagen, die ganze Fabrikhallen mit Antriebsenergie für Maschinen versorgen konnten, waren die Auslöser der ersten industriellen Revolution. Mit fortschreitender Elektrifizierung konnte man elektrische Arbeitsstationen für Facharbeiter überall platzieren. Das war die zweite Revolution. Die dritte kam mit der Automatisierung von Arbeitsschritten durch CNC-Maschinen (Computerized Numerical Control) und Industrieroboter – einmal durch einen Spezialisten eingerichtet, können diese Gerätschaften manchen Facharbeiter ersetzen.
Auf ein Neues
Die tragenden Säulen der anstehenden vierten Revolution sind zunehmend autonome Roboter, wie im Artikel ab Seite 110 umrissen, Virtual, Augmented und Mixed Reality wie im Artikel ab Seite 114 sowie viele Ansätze zur Mustererkennung, etwa im Interesse der vorausschauenden Wartung. Sie ist Gegenstand des Beitrags ab Seite 116.
Die Vision hinter dem Begriff Industrie 4.0 sieht vor, mit den heute verfügbaren IT-Mitteln schneller auf individuelle Kundenwünsche zu reagieren und vorhandene Ressourcen besser auszulasten. Als Fernziel steht die Idee einer menschenleeren Fabrik im Raum, in der Roboter autonom auf jede Situation reagieren und sich Auftrag für Auftrag zusammentun, um alle Arbeitsschritte zu erledigen. Dieses Konzept gehört aber heute nach Expertenmeinung in den Bereich Science-Fiction.
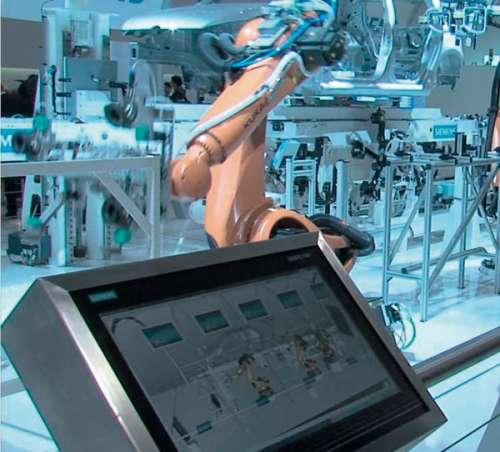
Als viel realistischer gilt das Ziel, alle Abläufe im Unternehmen möglichst lückenlos zu digitalisieren. Das verspricht zwei Vorteile: Erstens lassen sich die Daten kontinuierlich miteinander synchronisieren, sodass etwa der Vertrieb seine Angebote jederzeit am aktuellen Rohwarenbestand und am Auslastungsgrad des Maschinenparks ausrichten kann. Zweitens kann man die jederzeit abrufbaren Daten für ganz neue Geschäftsmodelle verwenden.
Das Fundament steht
Zu einigen Zielen von Industrie 4.0 gibt es bereits erfolgreiche Pilotprojekte:
– Roboter folgen nicht mehr streng einer starren Programmierung, sondern agieren zunehmend autonom. Ein Gerät in einer Fließbandanlage erkennt am angelieferten Werkstück, ob es dieses nach Plan A oder B bearbeiten soll – dadurch kann eine Anlage auch kleinste Serien bis zur Losgröße 1 mit individuellen Merkmal-Kombinationen produzieren, ohne dass man sie dafür erst umrüsten müsste. Wenn die Vertriebsabteilung jetzt einen Auftrag nach Plan A erhält, braucht sie den nur noch an die Anwendungen für Warenwirtschaft, zur Produktionsplanung und zur Buchhaltung weiterzuleiten – den Rest wickelt die Fabrik vollautomatisch ab.
– Die automatische Mustererkennung in Kamerabildern hilft Robotern, sich in ihrer Umgebung zu orientieren. Die Bilder einer 360-Grad-Kamera lassen sich aber auch mit Zusatzinformationen aus der Auftragsbearbeitung, aus technischen Unterlagen oder mit Sensordaten anreichern und in Mixed-Reality-Brillen der Mitarbeiter wiedergeben. So kann etwa ein Spezialist vom Hersteller-Standort aus alle Details einer defekten Maschine beim Kunden mit seinem AR- oder VR-Headset besichtigen und gleichzeitig Informationen über Messdaten und Historie des anvisierten Teils einblenden.
– Viele Daten eines digitalisierten Industriebetriebs stammen von vernetzten Maschinen, sprich: aus dem Internet of Things. Das IoT konfrontiert die Datennutzer mit zwei Herausforderungen: Zum einen müssen ganz verschiedenartige Gerätschaften von unterschiedlichen Herstellern miteinander kommunizieren können und zum anderen muss man die Datenflut noch zu konkreten Aussagen verdichten. Die erste Aufgabe verliert gerade an Bedeutung, da sich das quelloffene Kommunikationsprotokoll OPC/UA für die Machine-to-Machine-Kommunikation durchzusetzen scheint.
Ganz anders verhält es sich mit der Datenanalyse: So leicht, wie man die Warenkörbe aller Amazon-Kunden nach Schema F in Kaufempfehlungen ummünzt, ringt man den Daten von zigtausend Sensoren einer Maschinenanlage keine relevanten Erkenntnisse ab. Solche Untersuchungen, etwa zur Optimierung von Prozessparametern, verlangen von Fall zu Fall eine individuelle Analyse. Solchen Anforderungen widmet sich derzeit eine wachsende Zahl von IT-Dienstleistern.
Risiken und Chancen
Die zunehmende Komplexität der verbundenen Systeme birgt gleich mehrere Gefahren des Kontrollverlusts: Damit eine Anlage aus vielen vernetzten Komponenten fehlerfrei funktioniert, müssen sich bei ihrer Konstruktion viel mehr Fachleute abstimmen, als das früher erforderlich war. Probleme an den Nahtstellen sind schwer zu vermeiden – das altbewährte Prinzip „Alles aus einer Hand“ hat weitgehend ausgedient. Außerdem schafft die umfassende Vernetzung zahlloser Sensoren und Maschinen offene Flanken für Hacker-Angriffe.
Aus Herstellersicht verspricht eine digitalisierte Fabrik anderseits massive Vorteile: verringerte Ausfallzeiten, geringeren Personalbedarf und die Option, ohne großen Zusatzaufwand auch bei der Serienfertigung auf individuelle Sonderwünsche einzugehen. (hps@ct.de)