Digitale Tiefkühlkammer
Ein Blick hinter die Kulissen des Mercedes-Entwicklungszentrums in Indien
Auch im tiefsten Winter sind Temperaturen von 25 Grad in Bangalore keine Seltenheit. Nicht gerade ein Ort, an dem man die Innenraumheizung neuer PKW-Modelle testen würde. Doch Mercedes Benz simuliert sich auf Rechenclustern einfach die Welt, wie sie dem Prototypen gefällt.
In der drittgrößte Stadt Indiens betreiben die Stuttgarter das größte Forschungs- und Entwicklungszentrum außerhalb Deutschlands. Im November 2016 feierte das Mercedes Benz Research & Develop Center India (MBRDI) 20-jähriges Bestehen. Zu diesem Anlass bekamen wir die Gelegenheit, einen Blick hinter dessen Kulissen zu werfen. Beim Betreten des MBRDI wird schnell klar, dass man hier keine großen Hallen mit Tonmodellen künftiger Karosserieformen oder spektakuläre Crashtests zu Gesicht bekommt.
Auf den rund 25.000 Quadratmetern wird überwiegend mit digitalen Simulationen gearbeitet. Damit ist man unabhängig von Umwelteinflüssen und Klimakammern. Um beispielsweise eine Heizung zu testen, werden die gewünschten Temperaturen im Computer vorgegeben. Ebenso ein gesitteter Verkehrsfluss, denn während auf den Straßen der überfüllten 8-Millionen-Metropole absolutes Verkehrschaos herrscht, tüftelt eine andere Abteilung auf einer simulierten Straße am Verhalten von Steuergeräten für autonomes Fahren.
Simulierte Taiga
Mit rund 600 von insgesamt 3500 Mitarbeitern nimmt die Simulationsabteilung den größten Posten am MBRDI ein. Außer naheliegenden Berechnungen wie etwa zum Crash-Verhalten werden hier auch diverse andere Eigenschaften künftiger Fahrzeuge simuliert – oft solche, über die sich ein Autofahrer niemals Gedanken machen würde. Eine davon ist den nordischen Ländern geschuldet: Stand ein Wagen über Nacht in Eiseskälte, müssen Heizung und Gebläse leistungsfähig genug sein, um die Windschutzscheibe innerhalb einer vorgegebenen Zeit abzutauen. In Zeiten vor Simulationen auf einem Rechencluster ließ sich so etwas nur durch Try-and-Error herausfinden.
Für die Entwickler waren solche Tests mit viel Aufwand verbunden. Nachdem das grundlegende Design und die Materialien eines Autos feststanden, musste ein Prototyp gebaut und anschließend in einer Kältekammer eingefroren werden. Falls Heizung und Lüftung nicht die gewünschte Leistung lieferten, hieß es „Zurück ans Reißbrett“, um anschließend mit einem modifizierten Prototyp einen neuen Test zu starten. Das kostet natürlich Zeit und Geld, weshalb es kaum verwundert, dass jeder PKW-Hersteller nahezu alle erdenklichen Eigenschaften am Rechner simuliert.
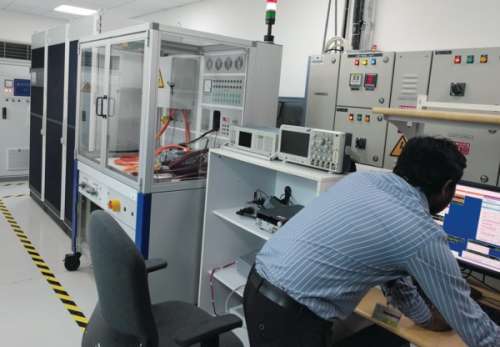
Bevor eine realistische Simulation überhaupt gelingt, werden zunächst unzählige Parameter und Rohdaten benötigt. So waren am MBRDI etliche Anläufe nötig, bis sich das Abtauen von Windschutzscheiben wirklich zuverlässig im Computer simulieren ließ. Für die Verfeinerung wurden die Rechenergebnisse immer wieder mit dem tatsächlichen Abtauen echter Autos verglichen. Mit jeder Iteration wurde die Genauigkeit der Simulation peu à peu verbessert. Nach etwa anderthalb Jahren des Testens und Abgleichens liefert der Computer laut der Entwickler nun so präzise Daten, dass für Enteisungsprognosen kein Auto mehr in die Tiefkühlkammer muss.
Außer der Zeitersparnis haben Simulationen noch einen weiteren Vorteil. So lassen sich viele Tests schon durchführen, wenn noch gar nicht alle Entscheidungen zur Realisierung eines Prototypen gefällt sind. Das verhindert grundlegende und damit teure Änderungen in späteren Entwicklungsstadien.
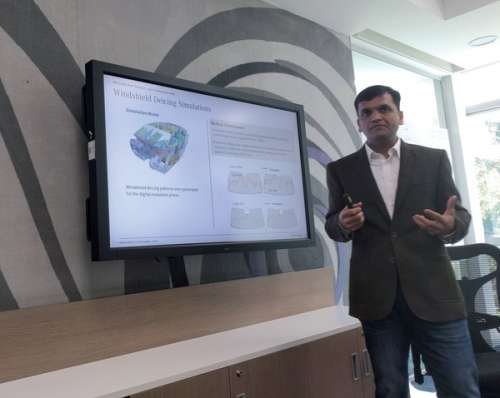
Um Sackgassen bei einer Neuentwicklung von Anfang an zu vermeiden, wird am MBRDI zusätzlich zum Abtauen auch die gesamte Innenraumheizung simuliert. Das Ziel ist dabei, dass sich der Fahrzeugraum möglichst schnell und gleichmäßig aufheizt, ohne die Insassen dabei mit Zugluft oder rauschenden und säuselnden Luftverwirbelungen zu nerven. Selbst bei der Ausgestaltung der Scheibenwischer bleibt nichts dem Zufall überlassen: Bevor sie in Serie gehen, hat ein Computer akribisch die Menge des abgewischten Wassers berechnet.
Unterwegs auf digitalen Straßen
In modernen Autos gehen unzählige Assistenzsysteme dem Fahrer zur Hand. Deren Steuergeräte nehmen sich die Entwickler am MBRDI ebenfalls zur Brust. Ein vollständiges Auto wird für deren Programmierung ebenso wenig benötigt wie eine Straße. Für die Optimierung eines Notbrems- und Spurhalteassistenten wurde im Testlabor das Steuergerät des Autos auf ein Testbrett geklemmt. Statt realer Sensordaten wird die Fahrzeugelektrik mit fiktiven Werten aus einem handelsüblichen PC gefüttert.
Der Ingenieur sieht so auf einem Monitor, welche Straßen- und Verkehrszustände simuliert werden und auf einem weiteren Bildschirm, welche Daten das Steuergerät erkennt, wie es sie interpretiert und anhand dessen die Geschwindigkeit und die Lenkbewegungen des (in Wirklichkeit nicht vorhandenen) Fahrzeugs in Echtzeit anpasst.
Im Labor lassen sich so alle erdenklichen Notsituation – wie plötzlich vor das Auto laufende Passanten, stehende Hindernisse oder eine Vollbremsung des vorausfahrenden Fahrzeugs – mit wenigen Mausklicks simulieren und testen. Im Unterschied zu realen Testfahrten erspart das einen abgesperrten Parcours. Zudem lassen sich die wechselnden Verkehrssituationen mittels Computer viel schneller und vor allem gefahrlos für Mensch und Maschine ausprobieren.
Während unseres kurzen Besuchs klappte das Vermeiden eines Auffahrunfalls problemlos: Das PKW-Steuergerät interpretierte die vorgegaukelten Daten des fiktiven Radarsensors korrekt als ein auf der rechten Spur stehendes Auto und nahm zunächst Gas weg und betätigte schließlich die Bremse, um eine Kollision zu vermeiden.
Rauschen statt Rußen
Handfester ging es im Labor für Hochvolt-Technik zu. Unter dem sonoren Brummen mehrerer Trafos und Generatoren lief abgeschirmt hinter Schutzglas ein Elektromotor auf dem Prüfstand. Auf dem Kontrollmonitor davor überwachten Techniker diverse relevante Parameter wie die Temperatur, die Energierückgewinnung im Schubbetrieb, die Energieaufnahme und die vom Motor erzielte Leistung.
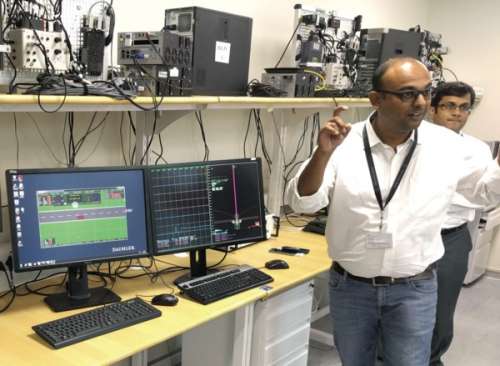
Aufgrund der potenziell tödlichen Gefahr im Umgang mit Starkstrom bekommen alle Ingenieure, die am MBRDI im Hochvolt-Labor arbeiten, vorab in Deutschland eine Schulung. An deutsche Sicherheitsstandards und Vorschriften hat man sich auch beim Aufbau des Elektrolabors gehalten. Notgedrungen – da es, wie man bei der Führung berichtete, in Indien derzeit noch keine Bau- oder Einrichtungsvorschriften für derartige Testlabore gibt.
In nächster Nähe
Mit einer Entfernung von mehr als 7.000 Kilometern und einer Zeitverschiebung von fünfeinhalb Stunden scheint Indien eigentlich nicht gerade der perfekte Standort für ein FuE-Zentrum zu sein. Doch Mercedes befindet sich dort in bester Nachbarschaft. In den vergangenen Jahren hat Bangalore sich zum „Silicon Valley“ Indiens gemausert: Quasi nur einen Steinwurf vom MBRDI finden sich Niederlassungen von Zulieferern wie Bosch, Siemens und Continental sowie IT-Größen und Chip-Hersteller wie Motorola, Dell, IBM, Intel und Texas Instruments.
Grund für die Attraktivität des Standorts ist unter anderem das große Angebot an Arbeitnehmern. Jedes Jahr verlassen Hunderte bis Tausende gut ausgebildete und ob der wirtschaftlichen Lage Indiens motivierte Informatiker und Ingenieure die Unis – Fachpersonal, das in Deutschland deutlich schwieriger zu finden und teurer ist.
Den Eindruck, dass in Bangalore günstige „Programmier-Drohnen“ gezüchtet werden, hatten wir bei unserem Besuch indes nicht: Das MBRDI ist eine hundertprozentige Tochter im Daimler-Konzern und bildet seine Mitarbeiter intern weiter. So will man unter anderem sicherstellen, dass das FuE-Zentrum wettbewerbsfähig bleibt und kein Wissenstransfer zur Konkurrenz stattfindet.
Offenbar scheint die Rechnung für Mercedes aufzugehen: Außer mit der Umsetzung von in Stuttgart angeschobenen Projekten kann das MBRDI mittlerweile mit nahezu 500 Patenteinreichungen aufwarten, wie dessen Leiter Manu Saale nicht ohne Stolz berichtet. (spo@ct.de)
Hinweis: Mercedes hat den Autor nach Bangalore eingeladen und die Reisekosten übernommen.